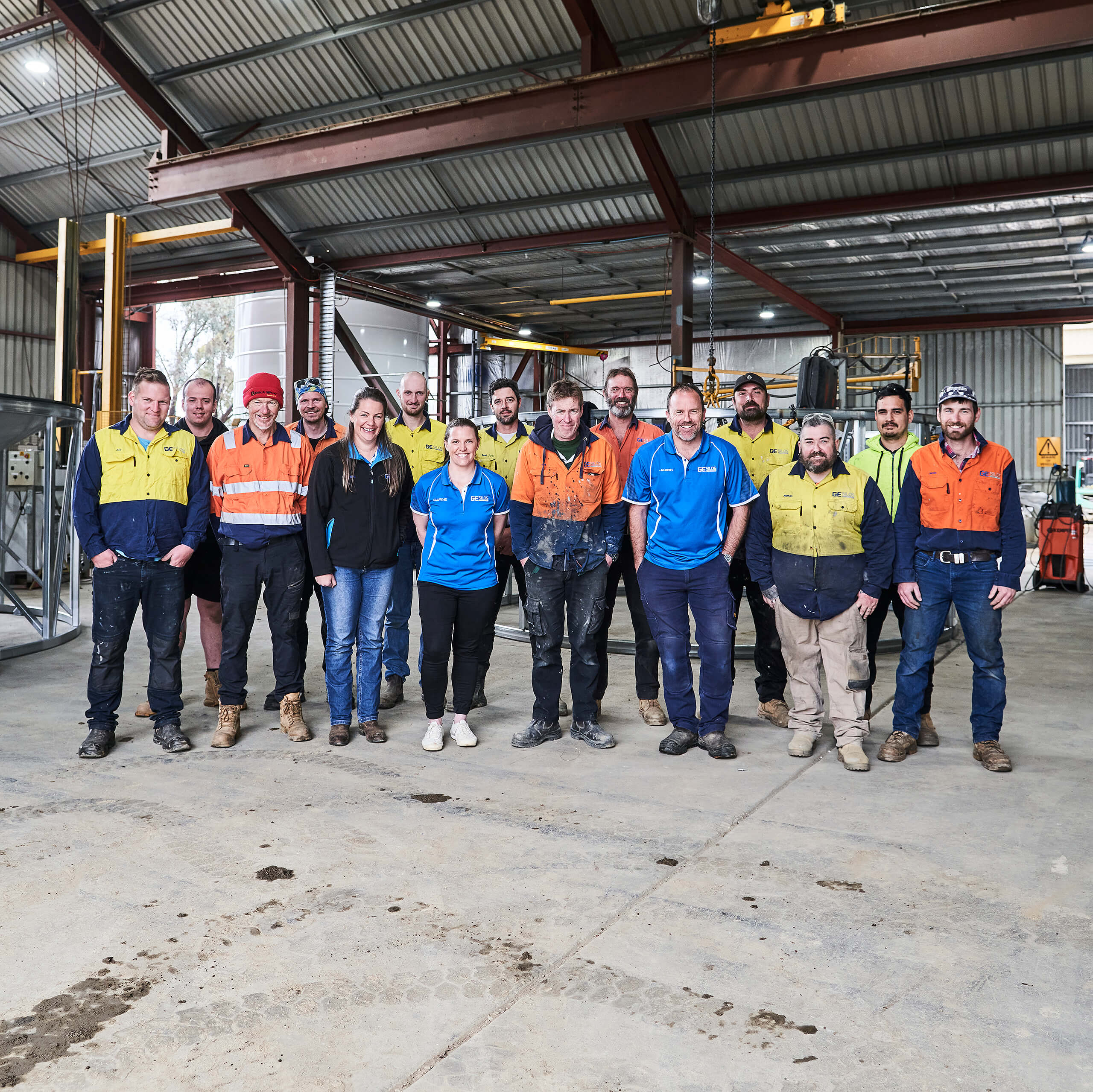
Pictured: the GE Silos team, November 2022
This is the GE Silos story…

An original Comer Brothers silo featuring early corrugated walls
It all began in 1978…
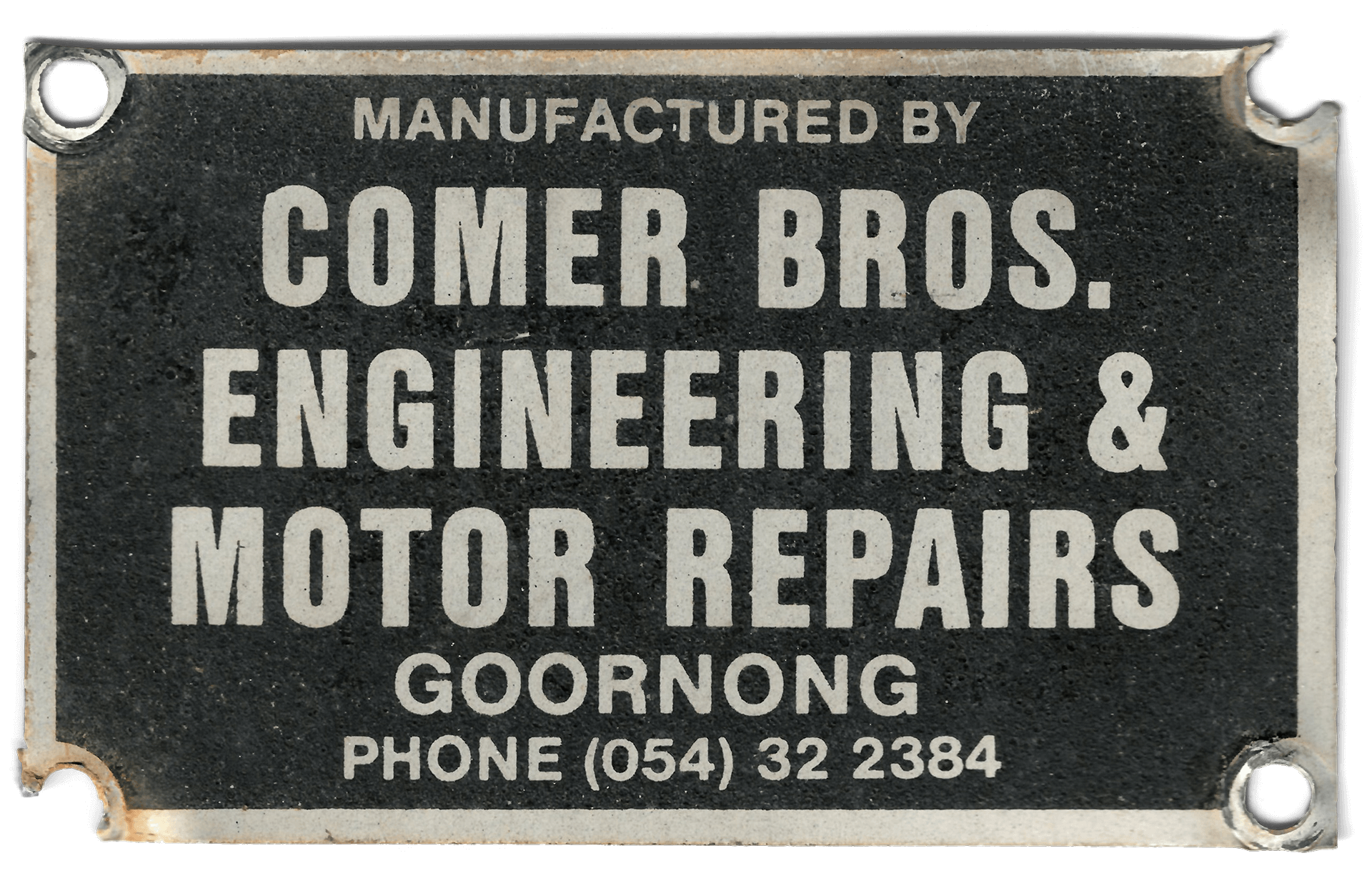
The GE Silos story begins in 1978 when Noel Comer and his brother, Brian, converted their father’s shearing shed into a workshop and began making and modifying farm equipment for the local farmers. Originally known as Comer Brothers, they quickly gained a reputation for building quality products.
Before long, Noel and Brian were approached to build a silo. Never ones to shy away from a challenge, the brothers took the project on. Theirs was an attitude of plucky optimism and despite being wholly under-equipped to build a silo from scratch, they got the job done!
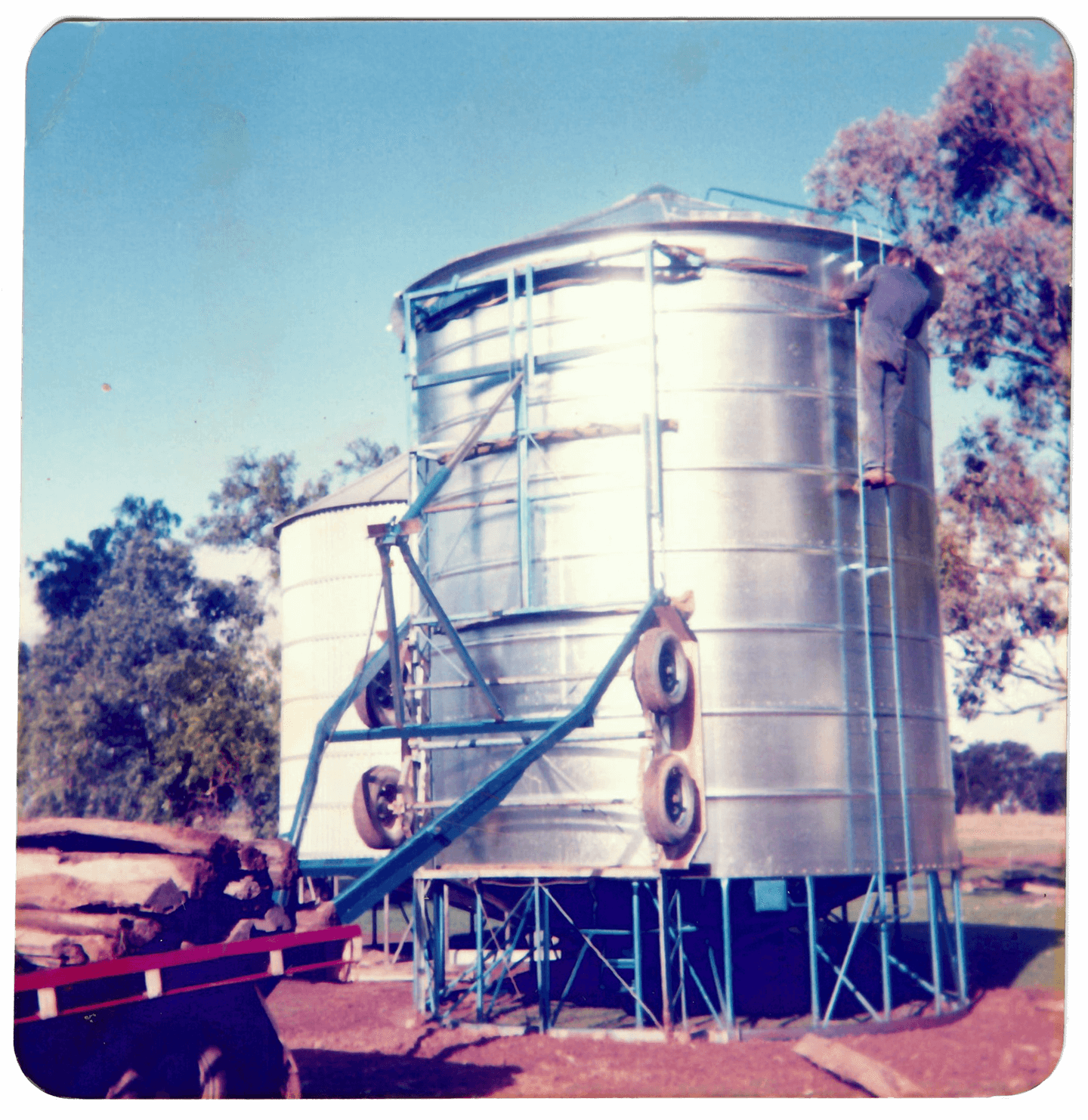
The job may have involved resorting to building the silo outside because the converted shed was too small, and working from a pallet precariously perched atop a forklift, but as it would turn out, the brothers had a knack for backyard engineering, and their silo did the trick!
Before long there was another request for a silo, then another, and another... it seemed there was something in this silo-making game.
Such was the quality of those early silos, we still see them in use on farms some 40 years later!
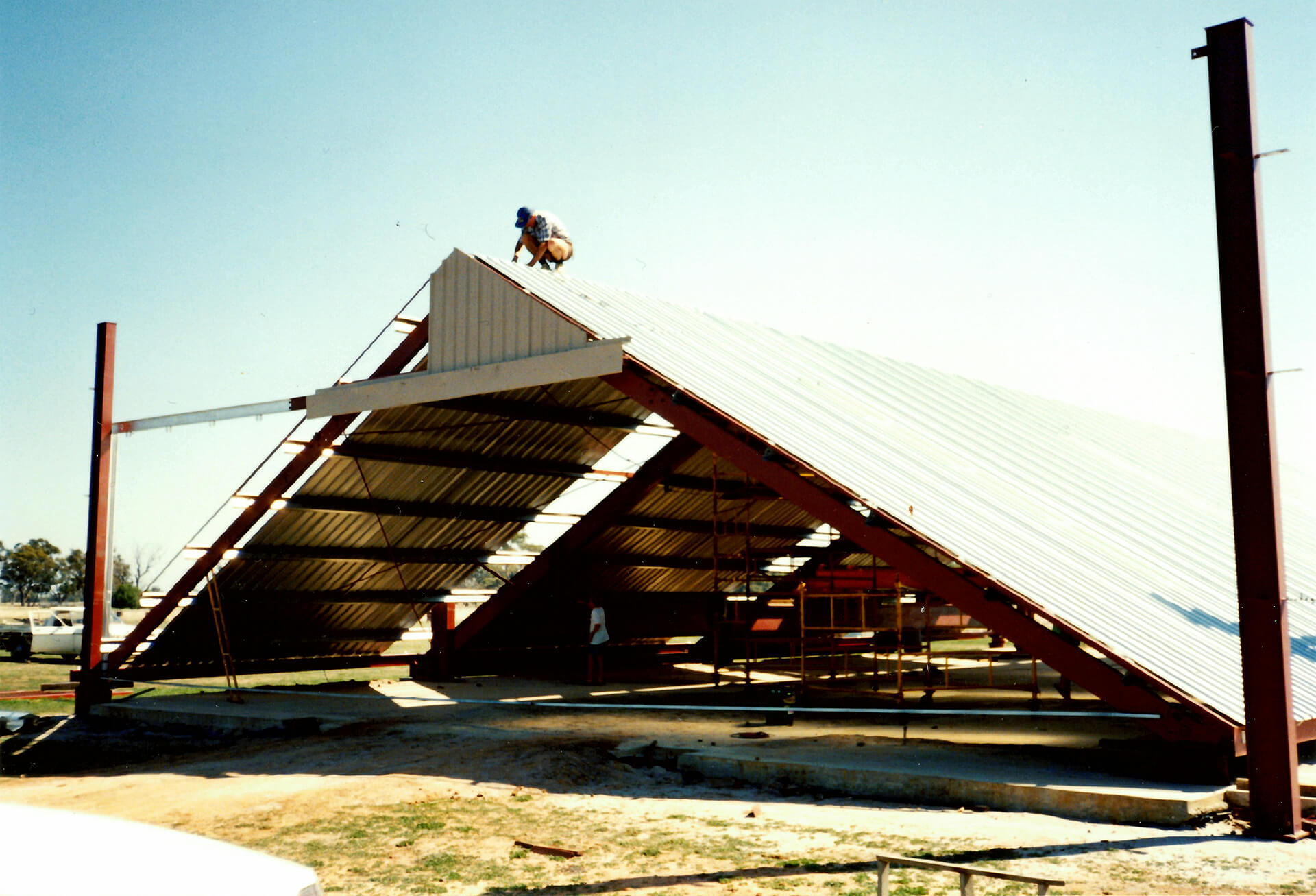
In 1996 we moved into our current site near Goornong in central Victoria.
And so GE Silos is born…
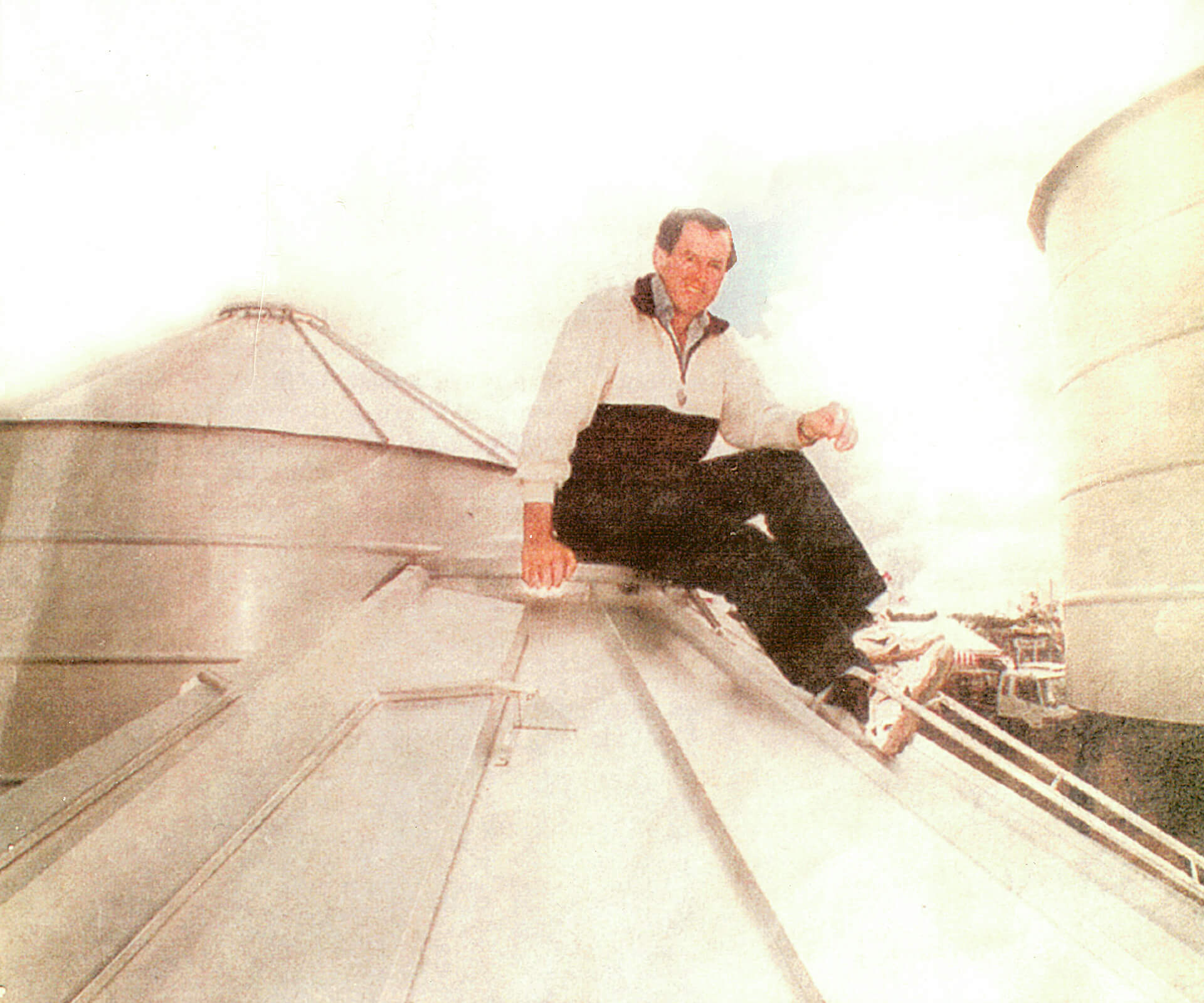
In 1989, the brothers decided to go in their own directions. Noel wanted to focus on designing and building silos and, along with his wife Lyn, registered Goornong Engineering and continued to build quality silos for the local market.
GE Silos grew steadily as demand for their high quality silos increased. Eventually they were outgrowing their current facilities and in 1996 Noel and Lyn built a new purpose-built factory at the current location, just outside of Goornong near Bendigo in Central Victoria.
The new shed was designed predominantly for fabricating silos and this was where GE Silos was born and really started to thrive. Over the years, Noel continued to improve and introduce new products as there was always something that could be made better.
A famously talented tinkerer, Noel personally custom-built the roller machine that curves the silo wall panels into shape. You wouldn't believe it if it wasn't true: but Noel's roller machine is still in use to this very day!
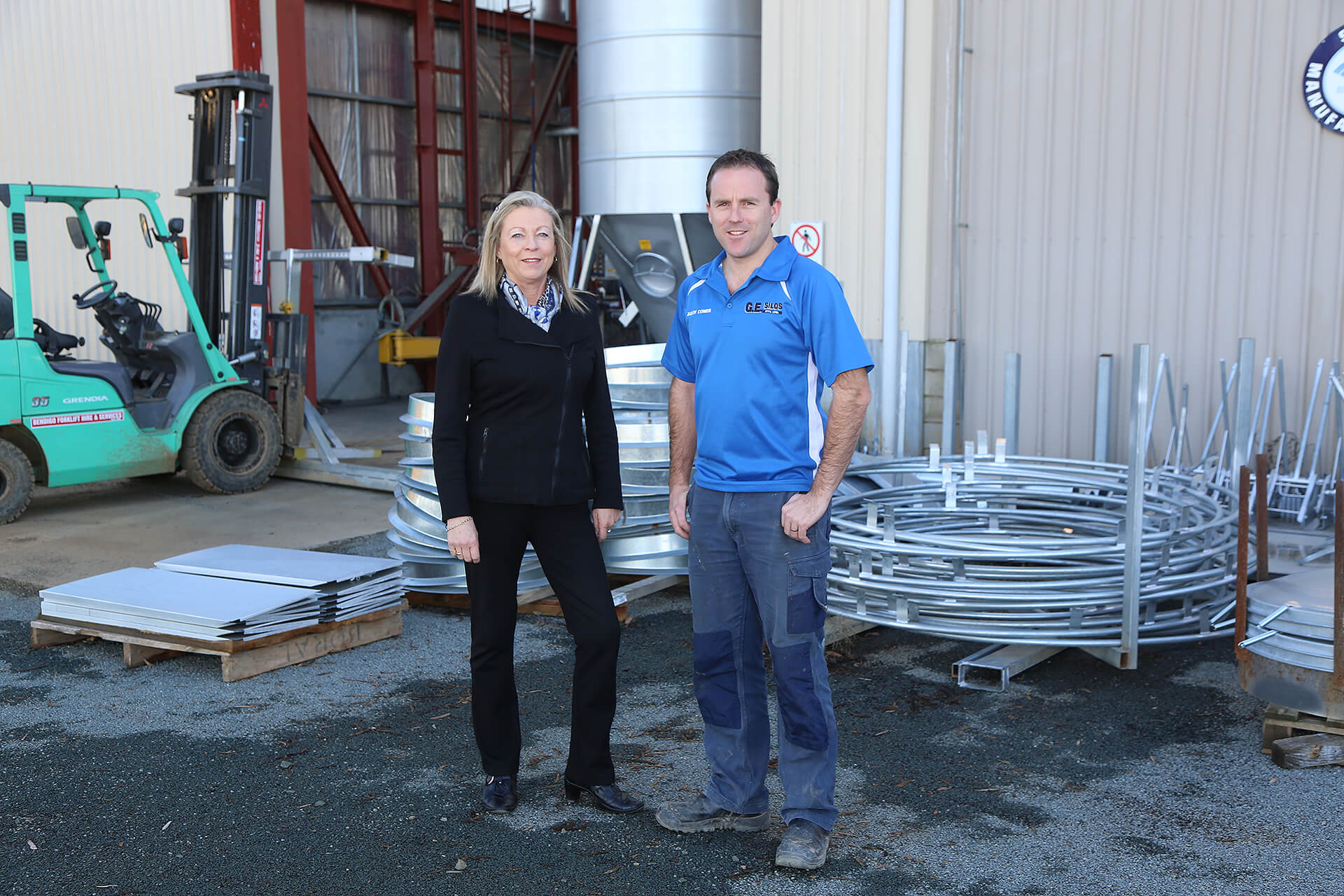
Lyn and Jason in 2003
The baton passes to the next generation…
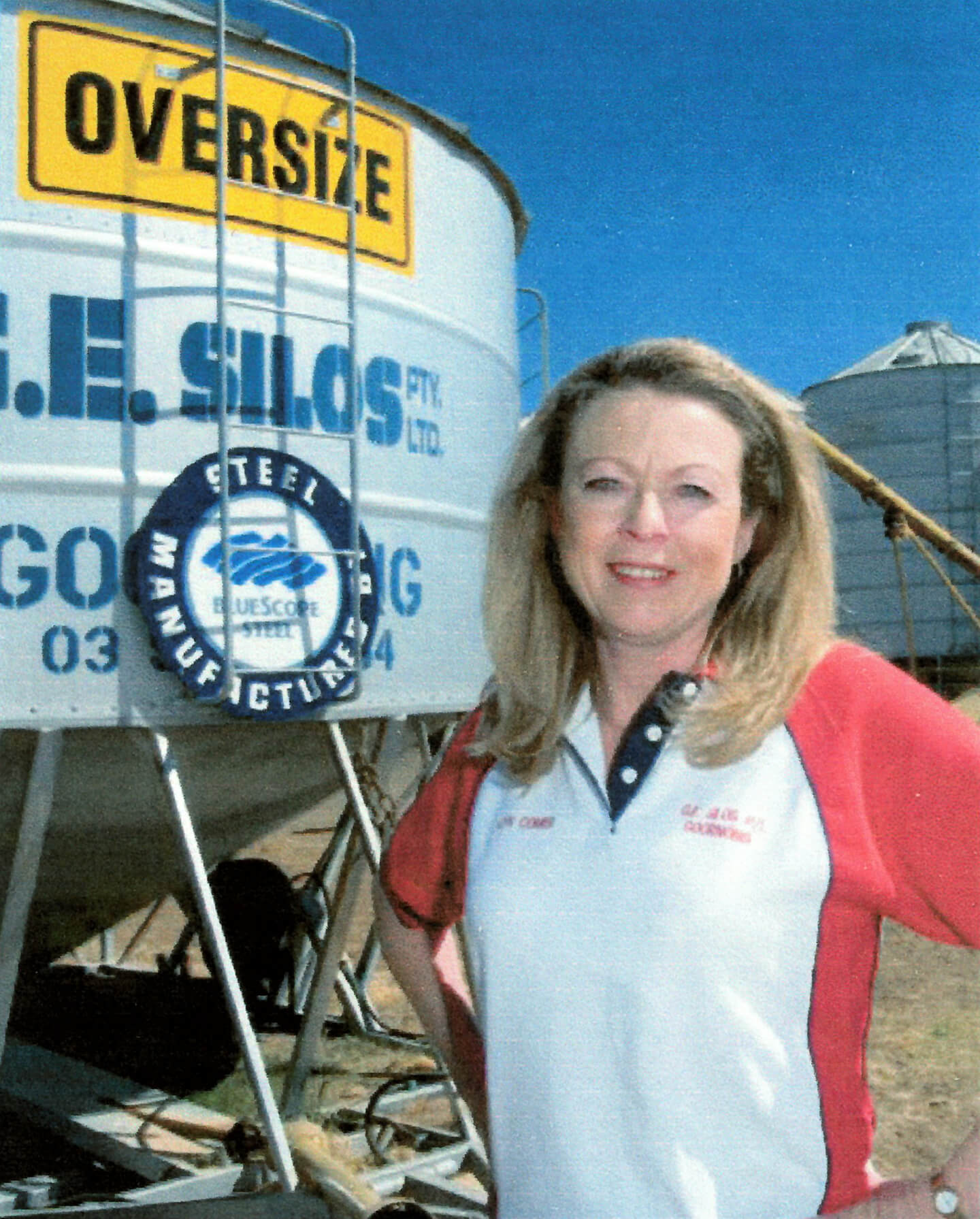
Over the remainder of the 1990s GE Silos continued to go from strength to strength. The new facilities and Lyn's involvement in the business proved pivotal in enabling the business to expand the product range and increase production as the millenium drew to a close.
Noel's son Jason joined the GE Silos during this time, showing a passion for management and bringing forth new ideas that would help move the business forward.
Sadly, in May 2001 Noel passed away after a short battle with cancer. Lyn and Jason continued to grow and develop the business, including increasing the largest silo produced from 65 tonnes to a whopping 110 tonnes, which necessitated the expansion of the factory in 2007: adding a 16 metre high tower to allow for construction of these larger silos.
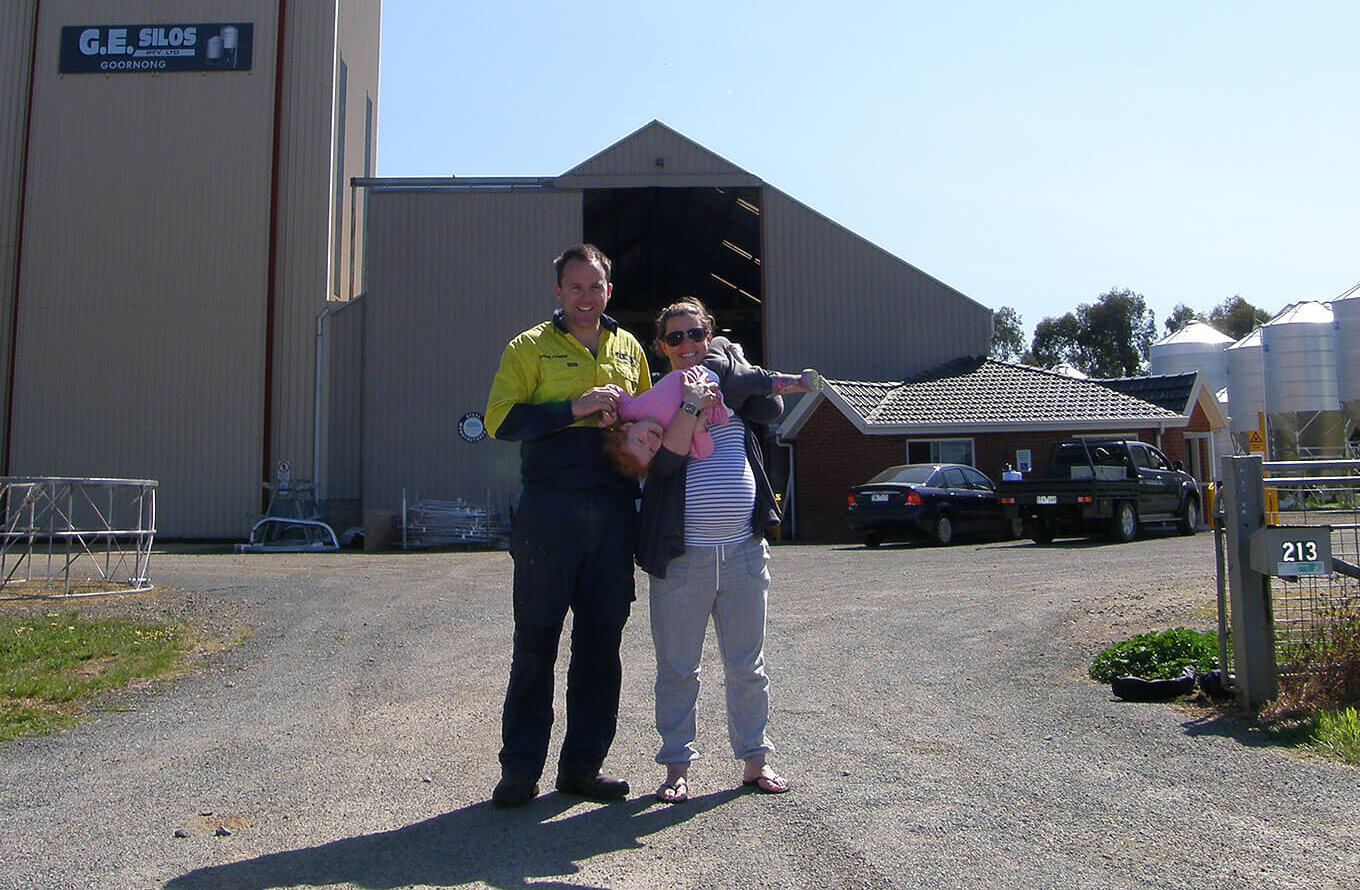
In 2015, Jason and his wife Carine purchased GE Silos from Lyn, taking the business into the next Comer generation.
Over the last eight years, Jason and Carine have continued to iterate and innovate, increasing overall silo production by 270% without compromising on the now-famous GE Silos quality and reliability.
And we have recently moved into producing heavy-duty fertiliser silos that required a number of major process changes to accommodate the super-thick silo walls and corrosion-resistant epoxy coatings.
The legacy lives on in 2023 and beyond
We like to think that Noel’s passion for enjoying life, being genuine, continual improvement, and always looking to help others, lives on in how we run GE Silos today. We are all so proud to be a part of a country Australian success story, and hope to pass our passion on to the next generation.
We remain passionate about innovating in silos and making our clients lives easier through excellent products and personal service.
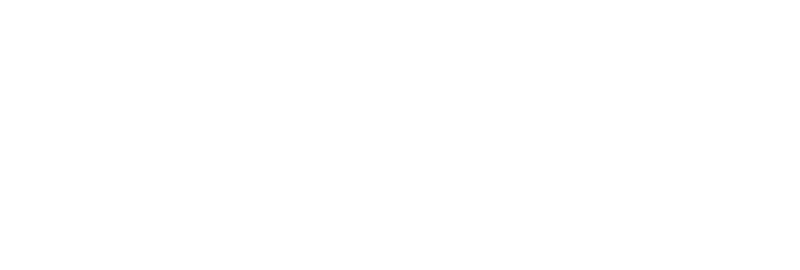
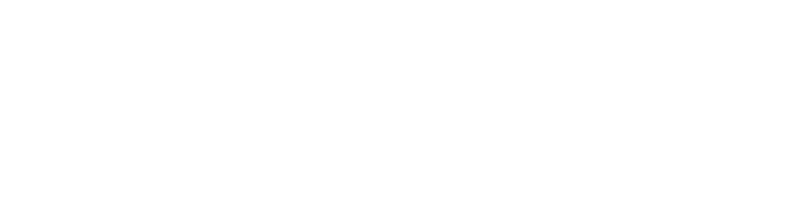
Our team is the heart and backbone of GE Silos.
GE Silos is one of those places where everyone looks forward to going to work each day. We work hard and stick to strict timelines and high production quality standards, but that doesn't mean we can't have fun at the same time!
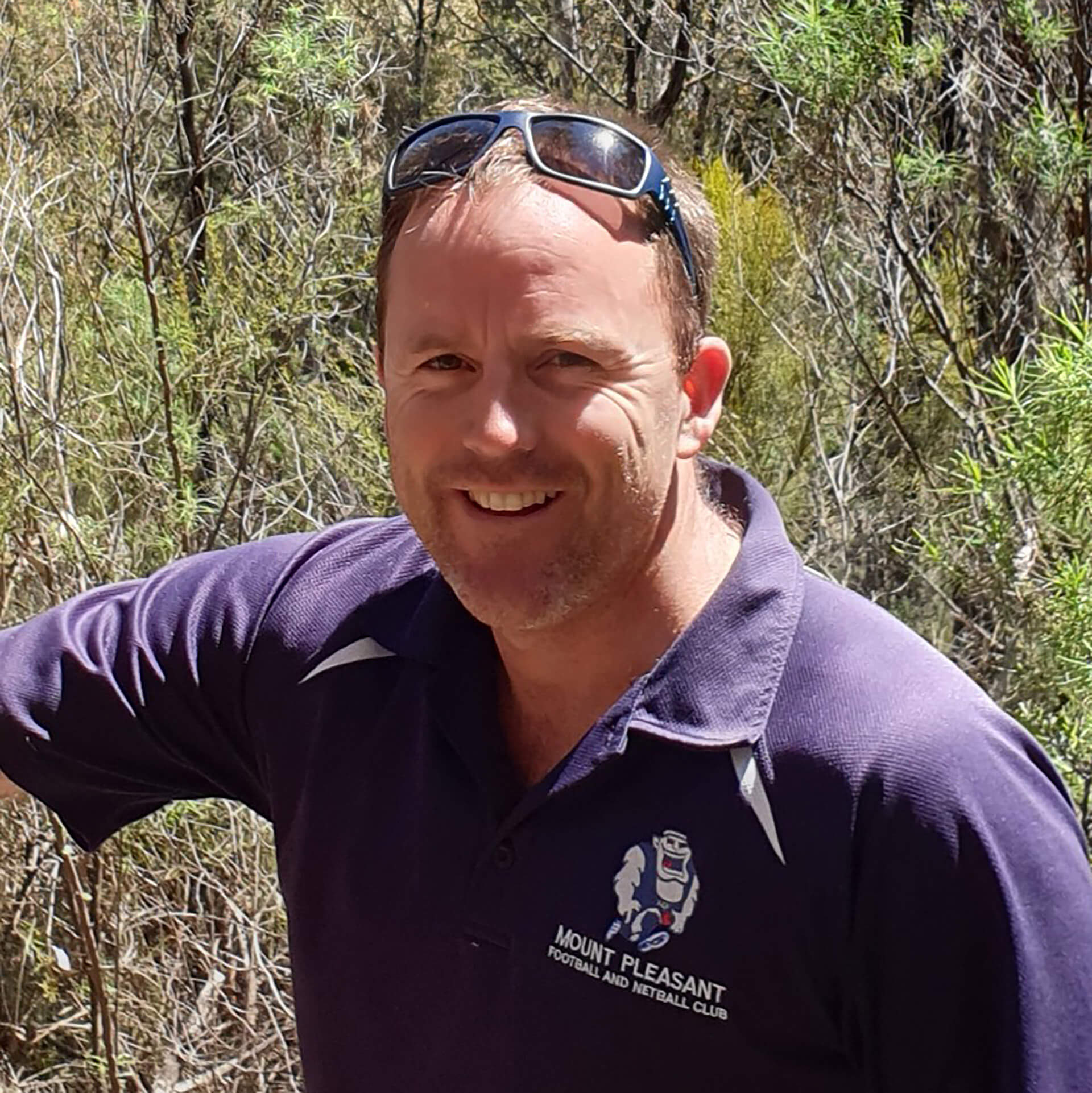
Jason Comer
Jason oversees all of the business operations. Jason loves boating with his family and playing table tennis.
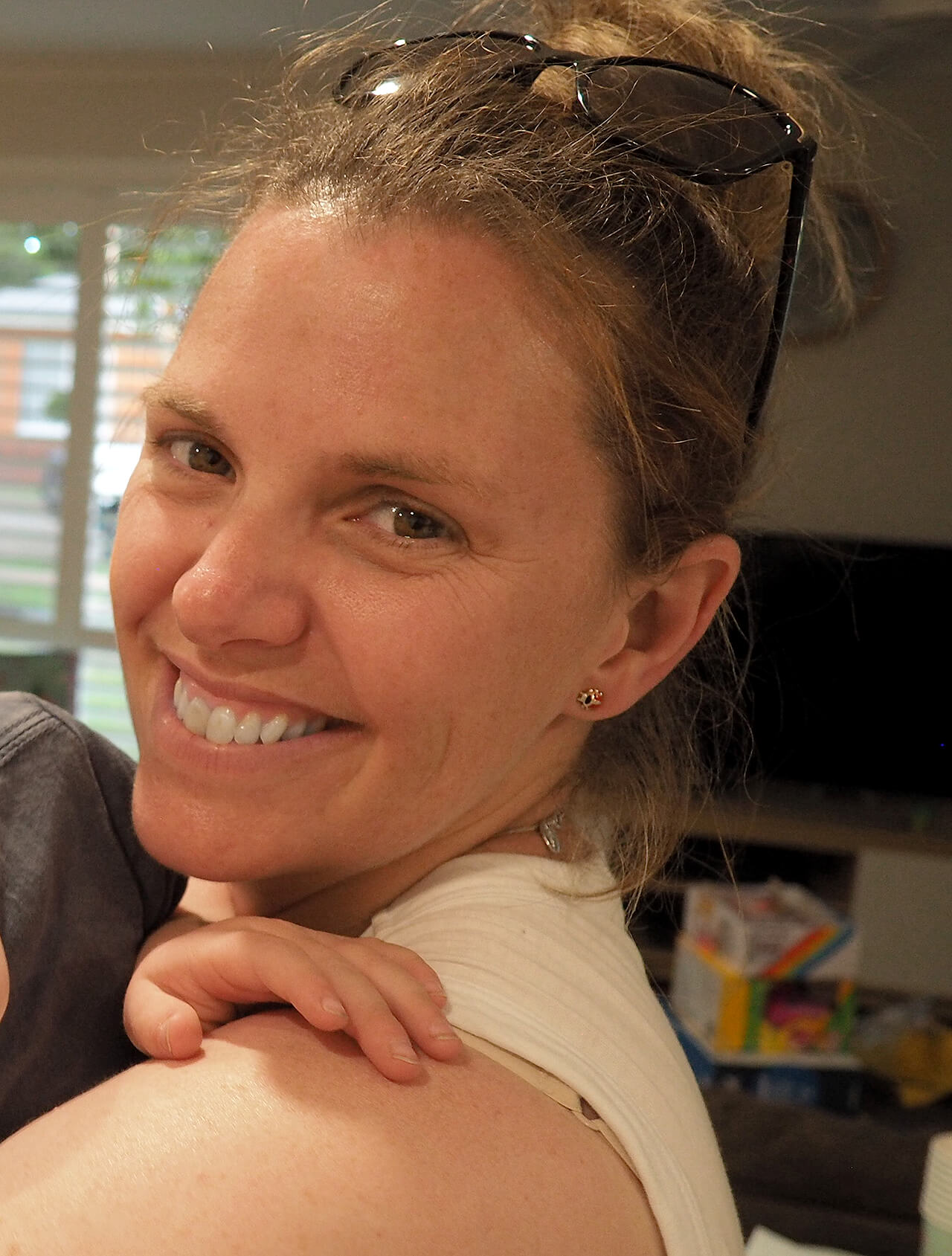
Carine Comer
Carine, along with her husband Jason is a Director of GE Silos. She oversees the Human Resources requirements of the company and enjoys working on the continual improvement of business. Carine is a mad Richmond supporter and enjoys getting outside and being active with her family
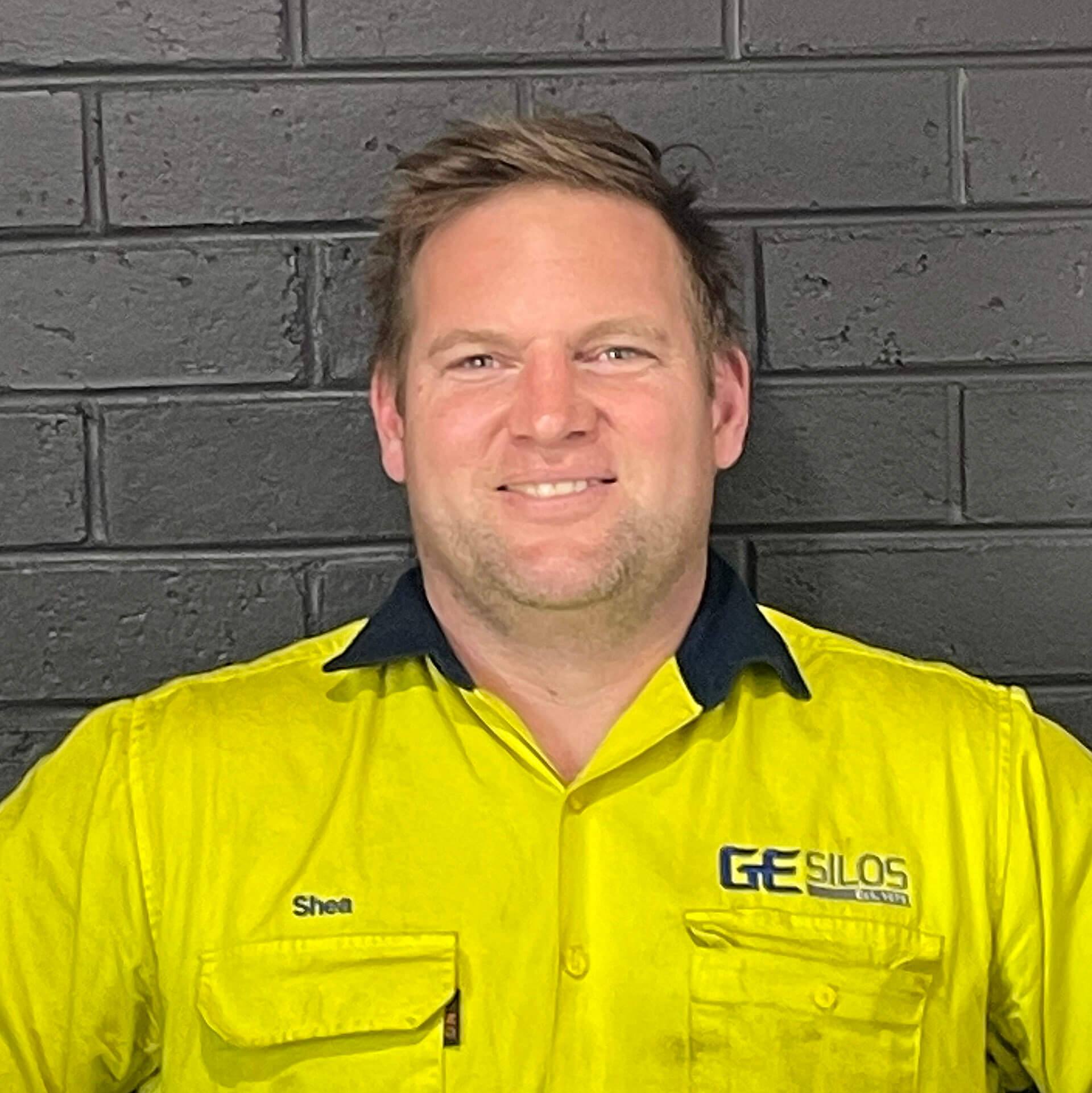
Shea Griffin
Shea manages our production team and keeps production running smoothly. Shea enjoys football, golf and spending time with family.
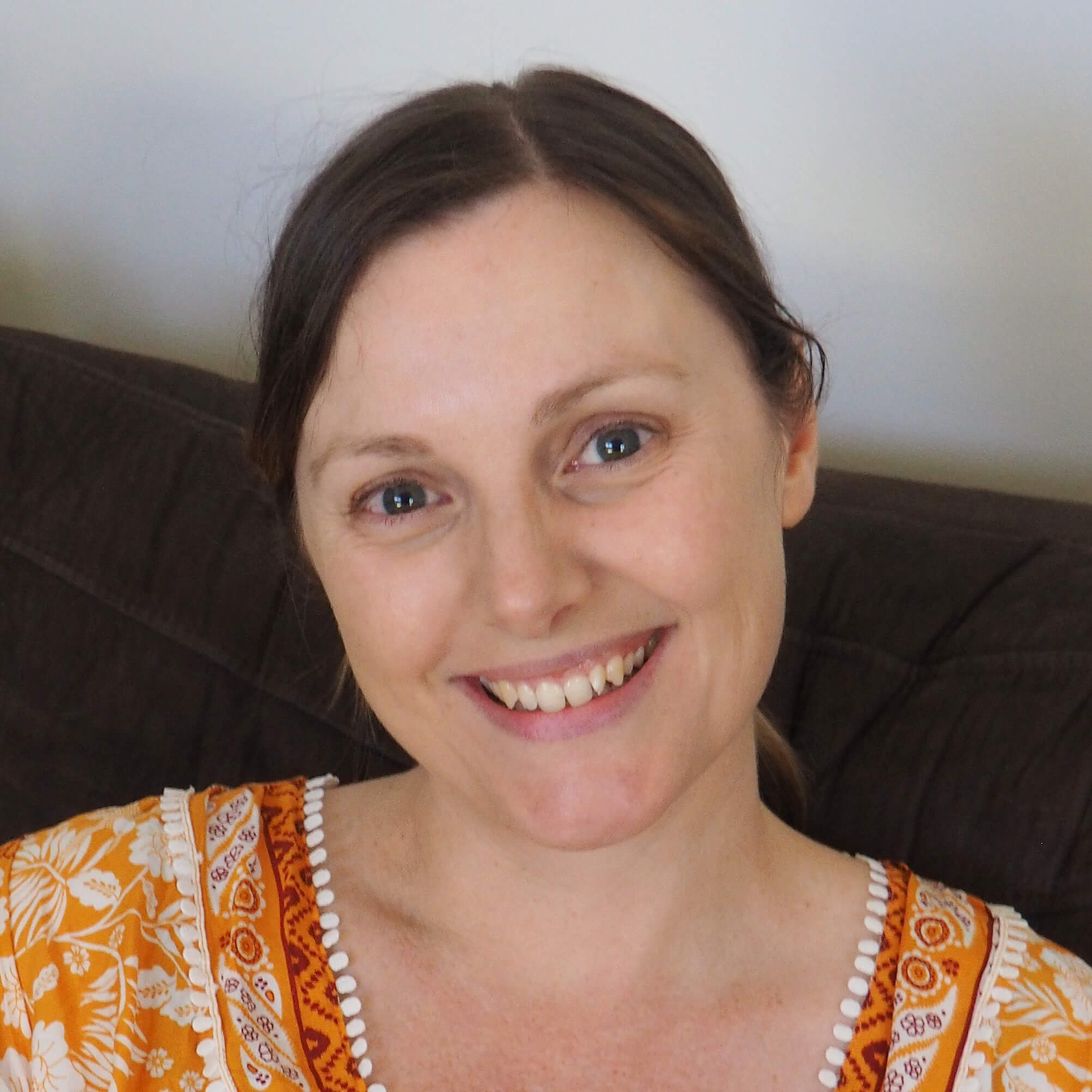
Nyree Hunt
Nyree is our Business Systems Officer, managing and updating the company’s management systems and also assists with the Human Resources requirements of the business. Nyree enjoys travel and spending time with family and friends.
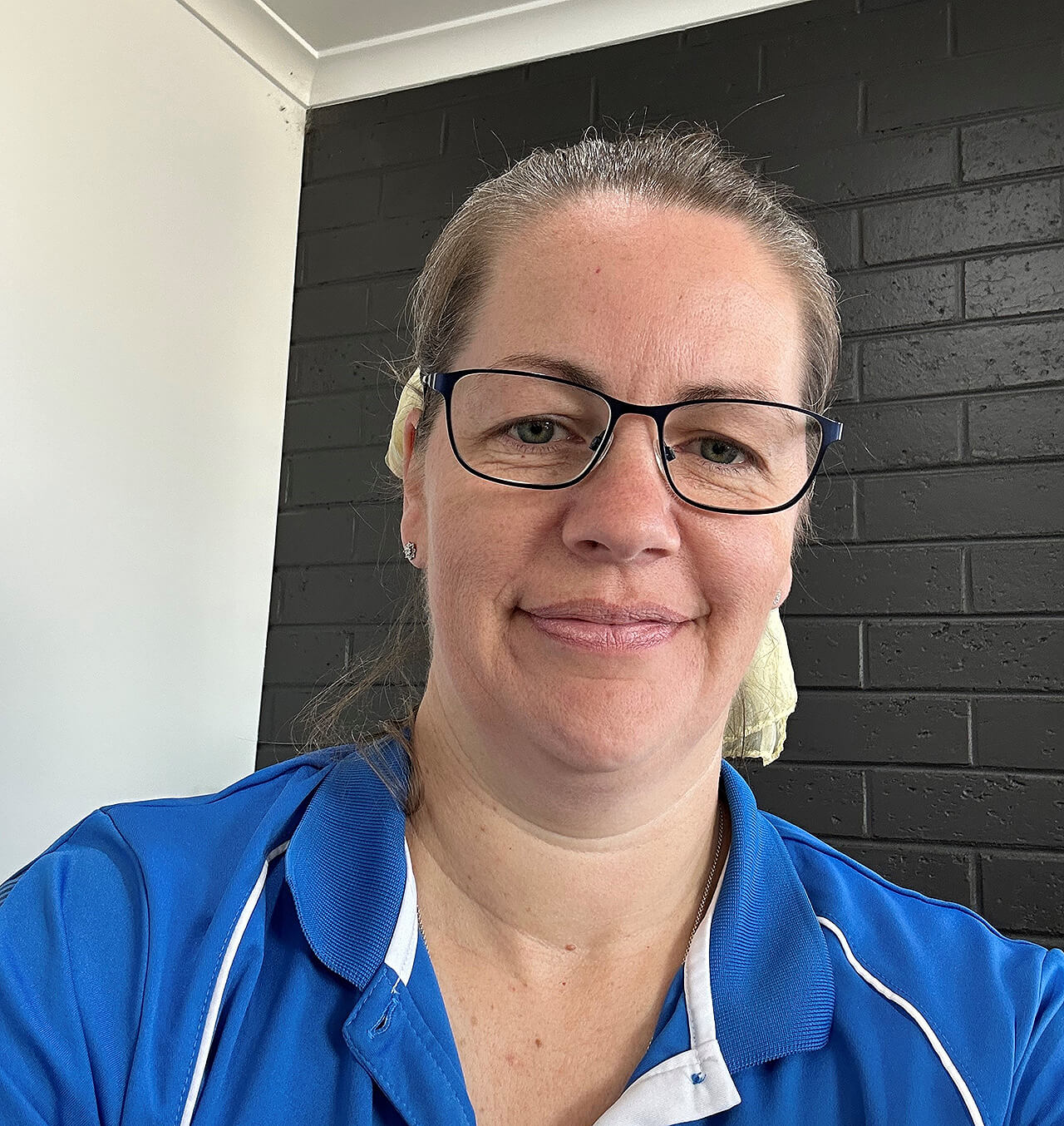
Karen Thompson
Karen is the main person you will talk to when you ring up or visit the office about your storage needs. Karen enjoys spending time horse riding, camping and spending time with her family and animals.
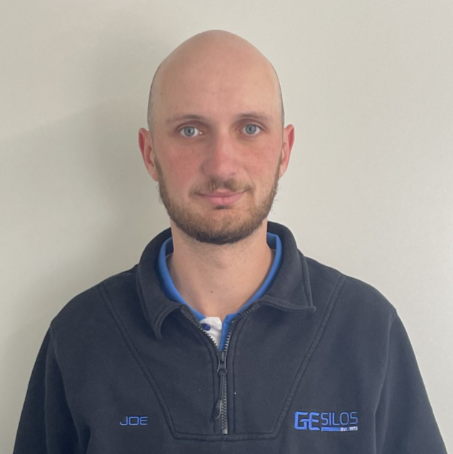
Joe McCormick
Joe is one of our qualified tradesman who also helps out with sales, marketing and OH&S. Joe enjoys playing sport and hanging out with mates.
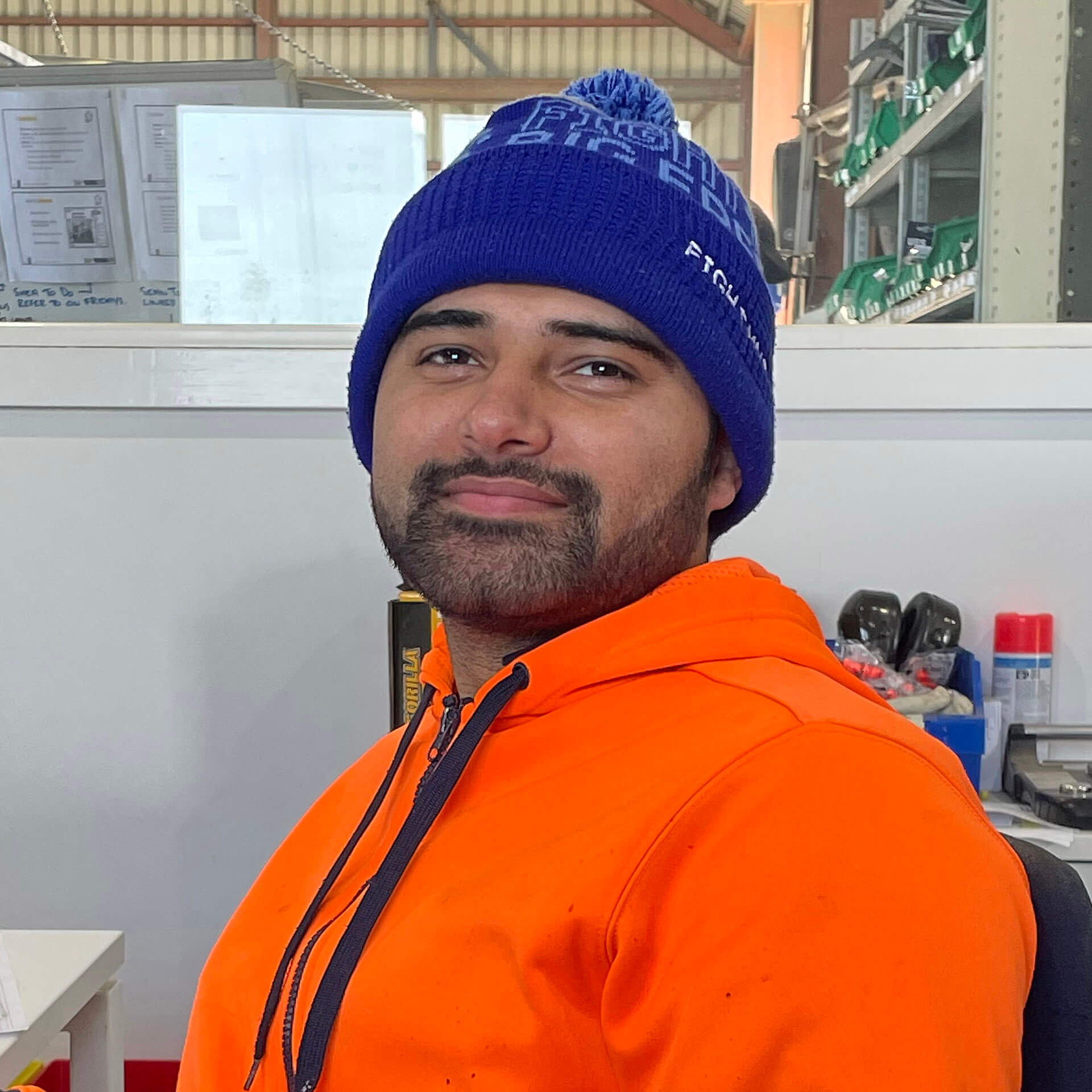
Akshay Delal
Akshay is our main engineer who helps improve our current products and works with clients to develop any custom needs they might need. Akshay enjoys heading back to Geelong on weekends to spend time with friends.
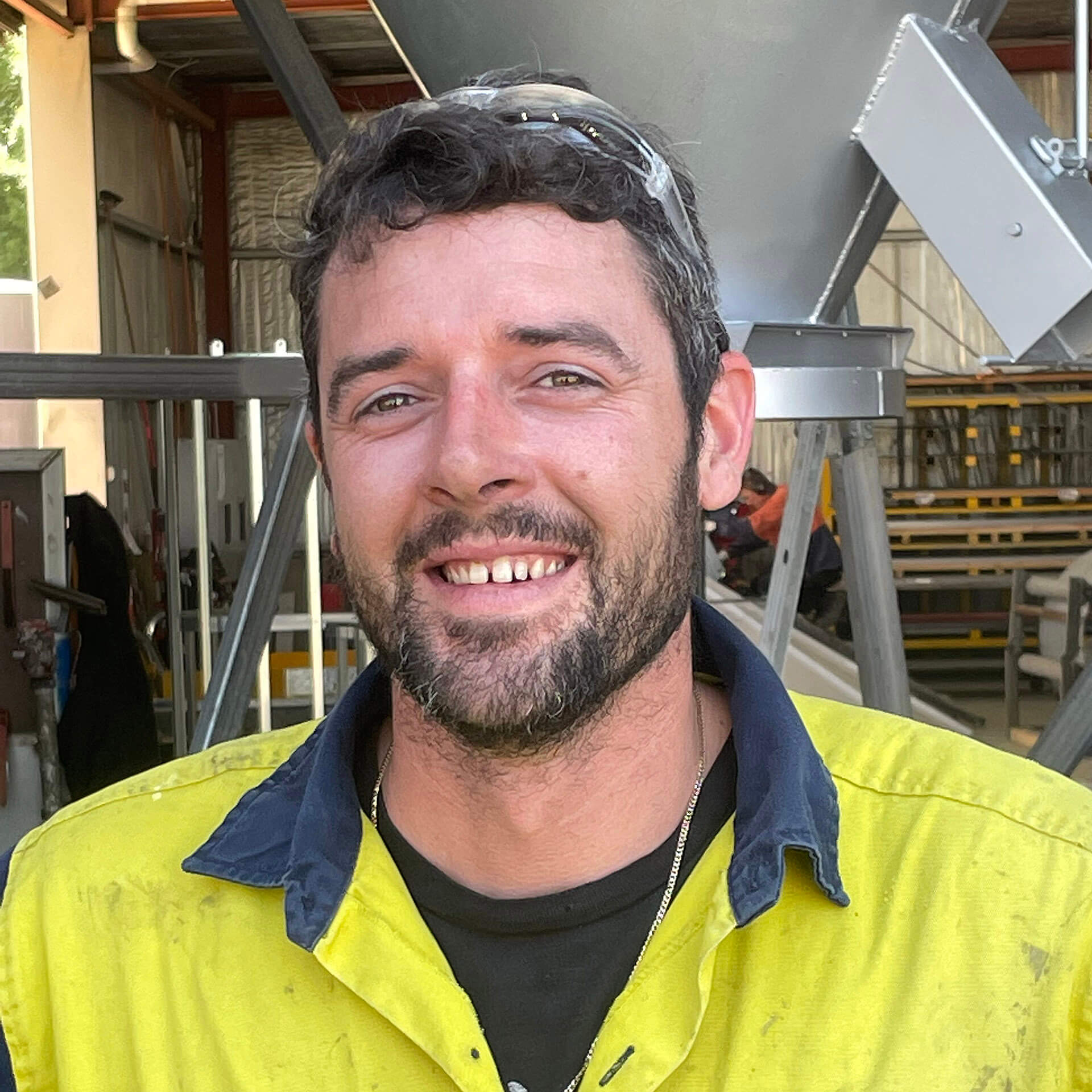
Sean Van Den Hurk
Sean is one of our qualified tradesman who is also our floor supervisor. Sean enjoys spending time outdoors with his family.
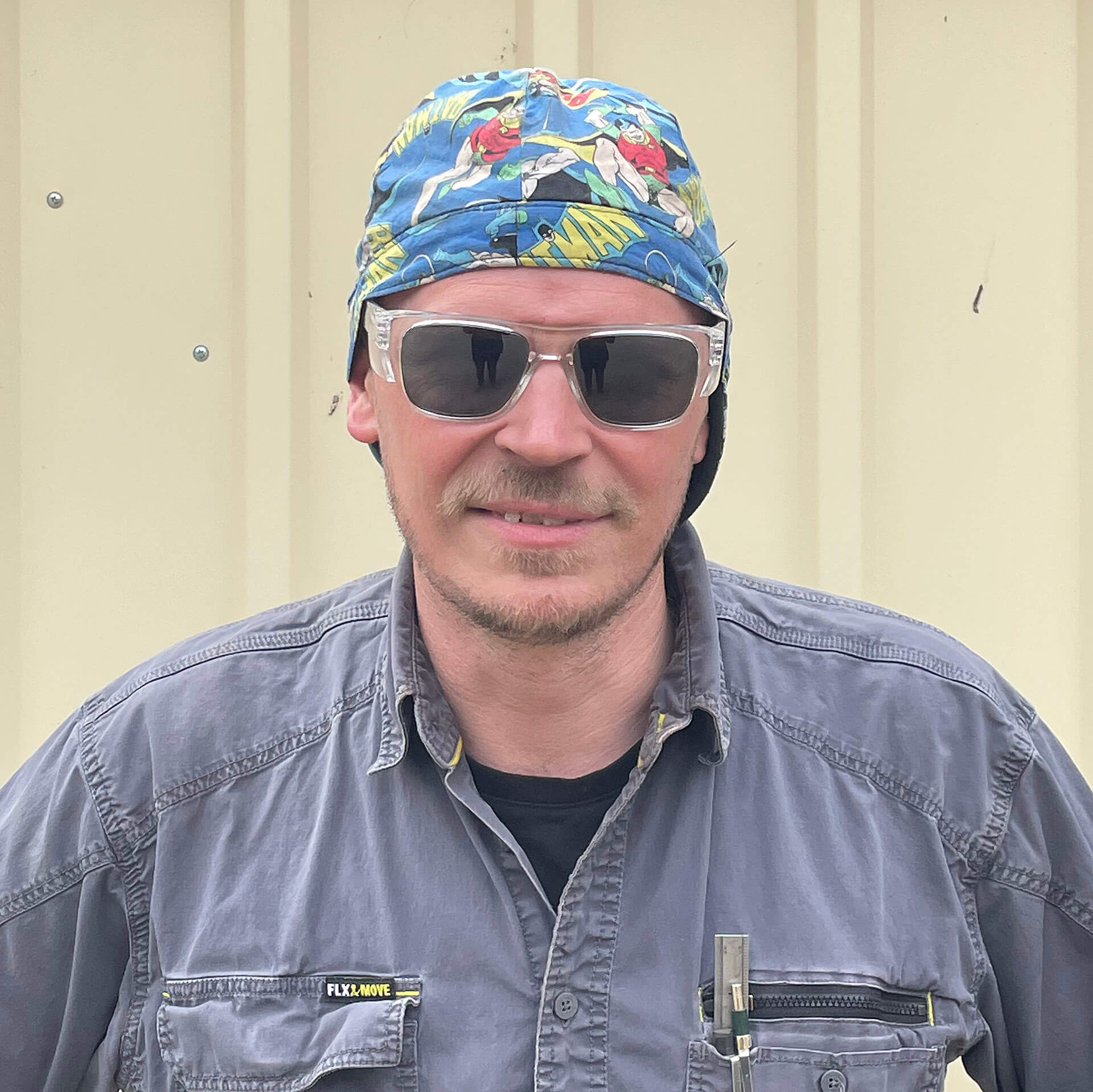
Brenton Hawkey
Brenton is our main fabricator of silo parts and general engineering jobs. Brenton enjoys spending his time going camping and 4wding.
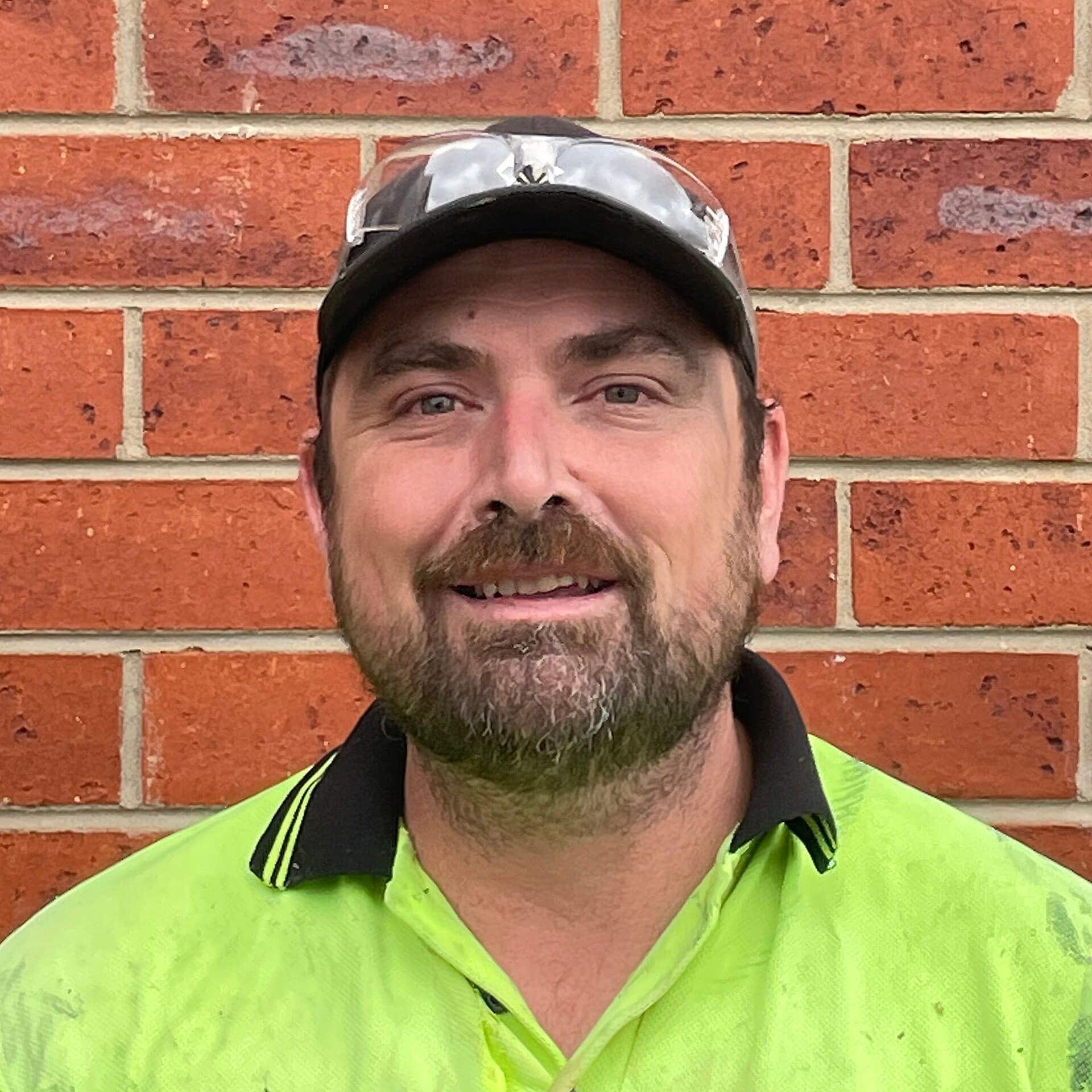
Marcus Nind
Marcus is one of our apprentices, who currently builds the bases of the silos. Marcus enjoys playing sport and spending time with his family
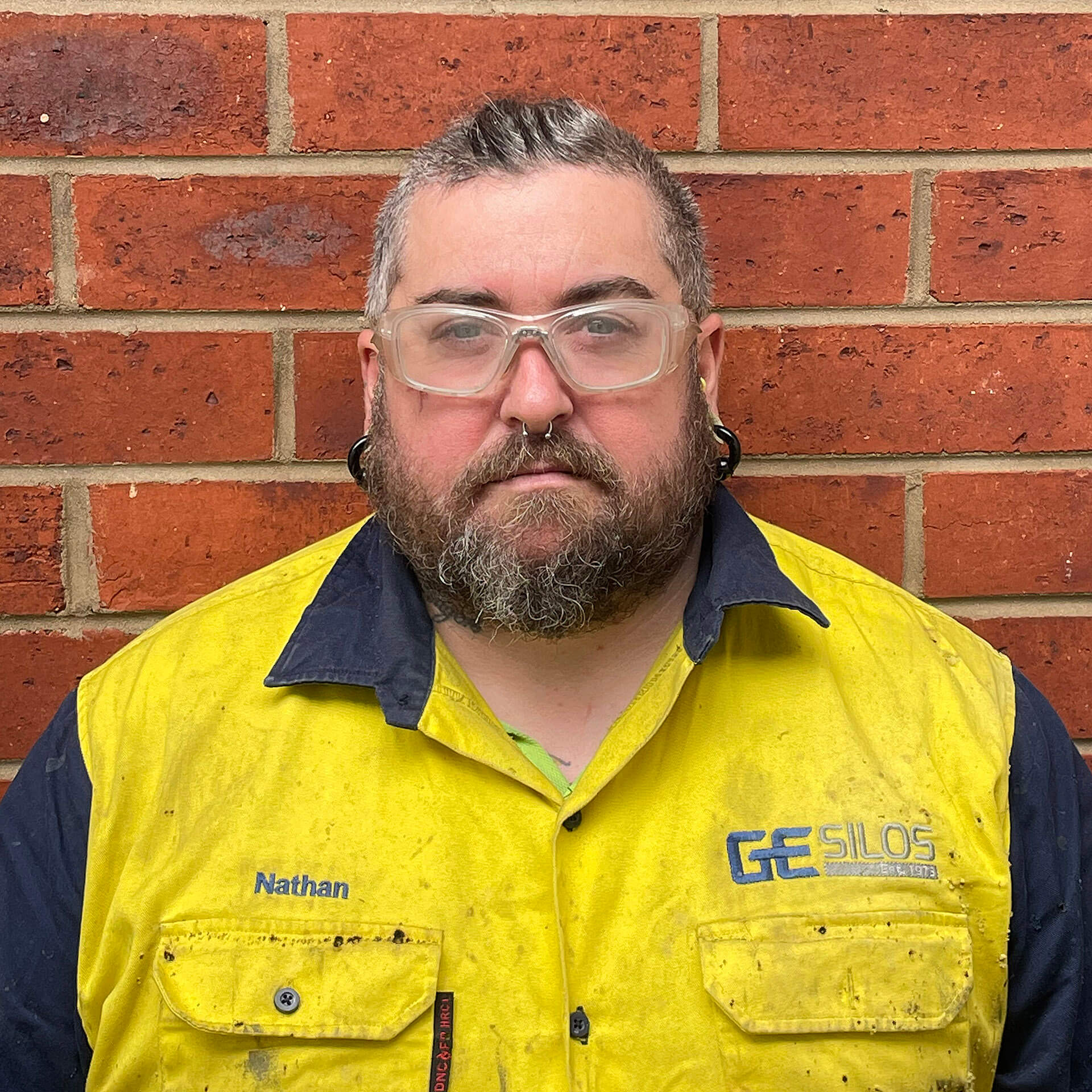
Nathan Eddy
Nathan is one of our apprentices who currently builds the base of the silos. Nathan enjoys riding motorbikes and spending time with his family.
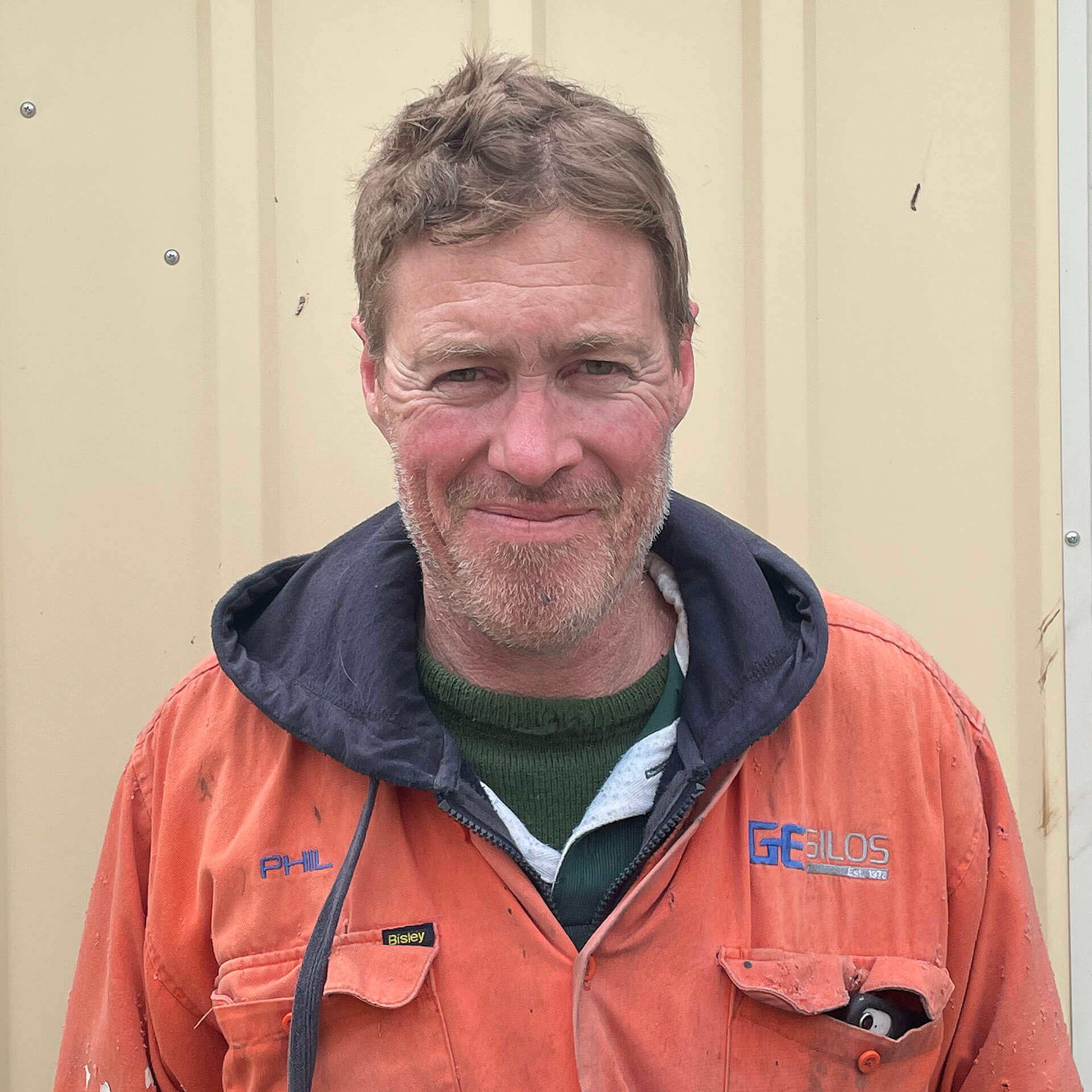
Phil Monks
Phil builds the roofs of the silos and helps with the manufacturing of parts. Phil spends his time doing projects in his shed and watching rugby.
Damien Cole
Damien is one of the newest additions to the team, Damien builds the tops of the silos while also helping to make parts from time to time. In his spare time Damien enjoys fishing, gardening and watching movies.
--Compressed.jpg)
Jim Coombs
Jim is our main Truck Driver who will deliver and set up your silo. Jim enjoys everything cars.
Ricky Boyd
Ricky is our newest delivery driver who comes onsite to install your silos. In his spare time Ricky enjoys tenpin bowling.
Over 44 years and counting, we’ve got building silos down to a fine art!
Our values drive our actions and our actions drive value for our customers.
Excellence
+
Superior Service
We are aware of our customers’ needs and provide the best possible products and services.
Responsibility
+
Accountability
We assume individual responsibility, measure outcomes, and continually improve.
Honesty
+
Integrity
We uphold a high standard of professional conduct and communications transparency.
Creativity
+
Innovation
We treasure new ideas, develop new ways of working, and challenge established norms.
Teamwork
+
Mutual Respect
We consider and accommodate the needs of our staff, customers, clients, and suppliers.
Community
+
Environment
We promote balance between business, community, and environmental sustainability.